Let’s take a look at some common inventory issues and how you can streamline the process.
Common Inventory Issues
Some common inventory issues include overstocking, shortages, clutter, and waste. Here’s how to avoid these problems and—if you already have them—how to best manage them.
Overstocking
Excess stock can be a threat to your organization’s bottom line. That’s because company capital has been invested to purchase it and money is being spent to store it. Oftentimes, overstocking issues can stem from improper tracking of the lifecycle stages of a product or poor management of demand forecasting and replenishment.
Shortages
Shortages can be equally as detrimental to your bottom line, as running out of a particular product in demand means lost sales. To avoid such a scenario, look at historical data to get a deep understanding of how much you can sell, and set a realistic safety margin based on it.
Clutter
Your warehouse can become cluttered and difficult to effectively work in when your inventory management system isn’t fluid. Reducing clutter will improve order fulfillment efficiency and allow you to easily find and account for inventory items.
Waste
Inventory waste can have multiple sources, including overproduction of goods due to anticipation of demand, poor storage practices leading to time wasted searching for products, and the inability to actively move inventory through your processes.
Streamlining the Process
First, it’s important that you understand how inventory flows in your warehouse. If you’re looking to implement a lean inventory management process, a demand-based flow is fundamental. This means inventory is only pulled when requested by a customer. Instead of solely relying on historical data, you’ll also need to actively monitor your inventory flow to make this approach work. This responsiveness will benefit you in many ways, allowing you to:
- Adapt and respond quickly to changes in the marketplace
- Keep your inventory at appropriate levels
- Prevent unnecessary storage costs
- Reduce write-offs of excess or obsolete inventory
Last but not least, you’ll need to commit your organization to continuous refinement of all your inventory tracking and management processes. This can result in improved efficiency, quality, cost and cycle time. Using a sophisticated system, Encompass Onsite is able to keep track of common inventory issues including overstocking, shortages, clutter and waste within an inventory. This allows us to streamline the process of making requests, ordering, issuing, and tracking said inventory. All said and done, our system makes automated reporting and record keeping a cinch, allowing your organization to focus on what it does best.
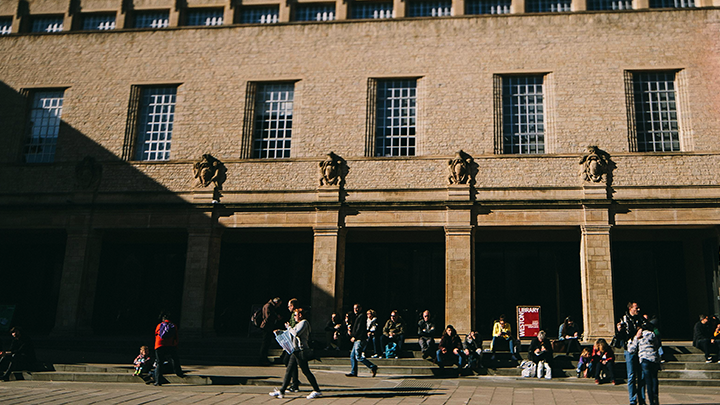
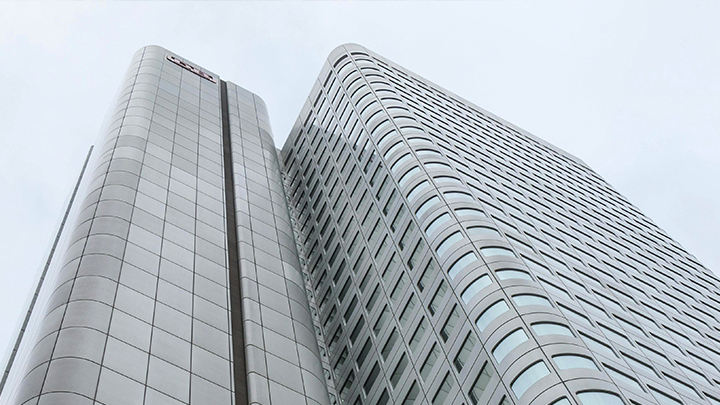
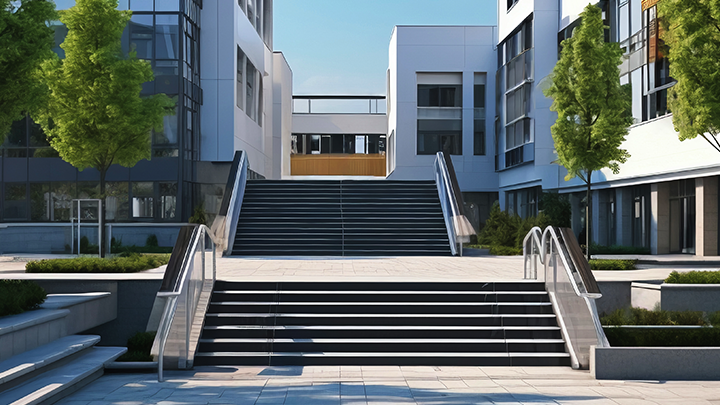
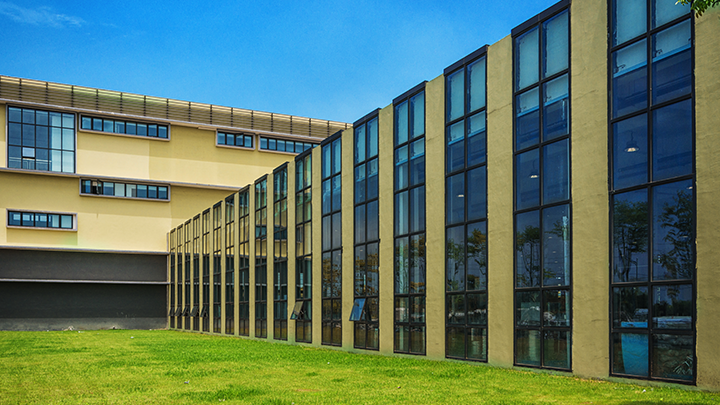
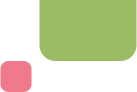
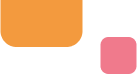
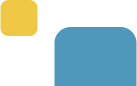
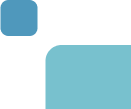